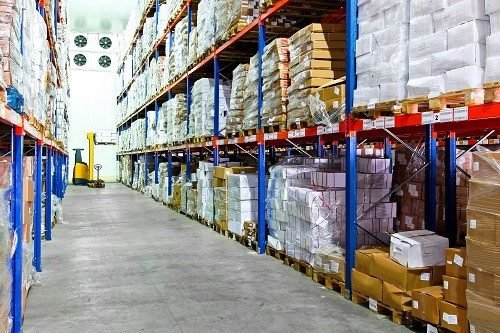
One of the most common methods of building warehouses at present time is currently the erection of buildings with the use of lightweight metal structures and thermal insulation with PUR or PIR panels. Their main advantages are short installation times, low capital and operating costs in comparison with the building from among the traditional materials.
Typically, the building of a cold warehouse includes the following stages:
1. Technical Assignment:
- formulating the needs of the client and drawing up a design specification on their basis
- carrying out of pre-project researches;
- design of the project;
- approval of the project;
- foundation erection;
- enclosing structures installation;
- roofing;
- making floor.
- utility lines installation;
- installation and pre-commissioning activities of the refrigeration equipment.
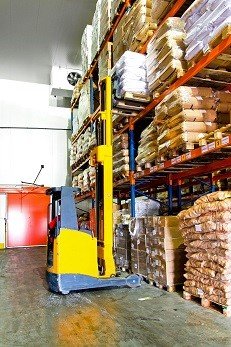
Technical Assignment
When contacting the company with a request for the construction of a refrigeratory warehouse, the customer cannot always present a clearly worded technical assignment. In this, the specialists, to whom he addressed, must help him. To obtain the technical decision and calculate the cost of construction it will be needed:- type of product;
- storage volume and product turnover;
- construction region.

Project
The project − a necessary component of any building, let alone a freestanding building. It is particularly noted that this is − a project that is made in accordance with your country current building standards, and simple the architectural and planning solutions drawn in the AutoCAD program are not enough. The last is useful for analyzing and approving the conceptual design of the building, but this is not enough to build it. So, for the safe use of the Refrigeratory warehouse, in the design, it takes into account the existing plot geology, the building area seismicity, wind and snow load, fire safety standards and much more, which is actually laid down in building codes and regulations. The disparity of finished object with building norms and rules or the requirements of fire inspection may cause additional costs for matching and reconstruction, or lead to the forced demolition of a building. For project implementation and pre-design works a topographic plan of the building area is necessary, a report on geological conditions, etc. As well as the permission of local administration for the building of the facility, without which it is formally impossible to begin the designing, let alone the building itself. The ready project is approved on the state instances, local administration and the customer himself. The further work, from the materials supply to the installation works, is carried out strictly on the project.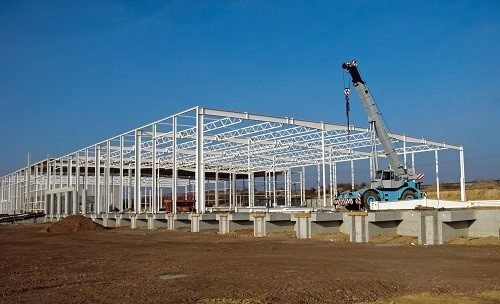
Building
The foundation type is chosen based on functional and economic requirements and constraints. In refrigeratory warehouses, the floor level, as a rule, is at the level of 1.2m from the ground for easy loading and unloading of products from cars and railway wagons. Simultaneously, it solves the problem of freezing through, due to the creating vented under-floor space, the absence of this requires the floor heating or performing the floor having a system of special channels, which leads to additional costs. When storing products, it must perform the specific requirements to the floor structure, so it must perform the functions of heat and waterproofing, withstand the planned load per unit area and the low temperatures influence, and also comply with sanitary standards in the refrigeratory warehouses. To solve all these problems, a multi-layered "pie" is making, the composition of which is also indicated in the building project.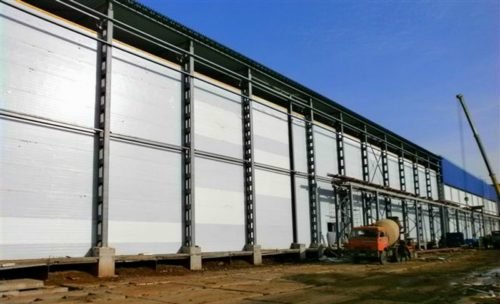
For example, the top layer of the floor is frost-resistant and non-dusty. And thanks to the special additives it is laid color in accordance with the functional features of the operation and the wishes of the customer. On the perimeter of the walls, the bump-side board is made, which protects the walls from damage during loading and unloading operations. The metal structures that make up the building frame must be protected from corrosion. The greatest value in the building of refrigerated warehouses has thermal insulation since it determines the refrigerator operating properties.
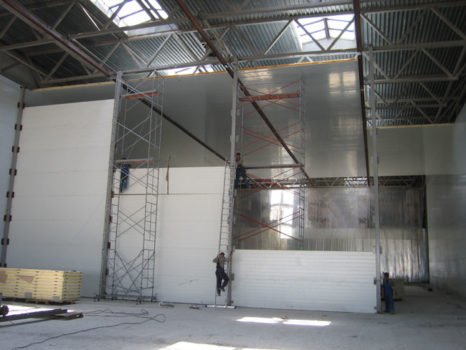
The thermal insulation is the subject of a number of rather stringent requirements:
- low thermal conductivity;
- low water absorption;
- heat resistance;
- low flammability;
- should not attract rodents and have sufficient mechanical strength.